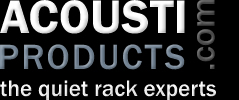



Products using these materials:
AcoustiPack Deluxe
AcoustiPack Standard
AcoustiPack SFF
AcoustiPack Antec Sonata I/II
AcoustiPack Antec Sonata I
AcoustiPack C6607
AcoustiCase C6607
AcoustiPack Antec 3700 BQE
Acousti Products use only highest quality professional studio-grade materials. They are formulated for acoustic effectiveness within the sound frequency range of 100Hz - 10KHz (which are those commonly associated with vibration and noise from hardware components). More details on sound performance.
"Imitation is the sincerest of flattery."
Charles Caleb Colton (1780 - 1832)
Our
acoustic materials have been copied by other companies since we originally
formulated them, so beware of cheaper alternatives! - especially materials that
can contribute to internal dust (called shedding), and also disintegrate easily
if scratched when fitting them.
Our products are certified to international flammability standards, and importantly, this includes the adhesives. It is the performance and quality of our materials that places our products at the higher-end of the market.
The majority of our acoustic material products are made from a
uniquely designed dual-layer composite material. This is comprised
of acoustic foam, composite adhesives and a dense acoustic barrier
mass layer. Information regarding these component materials is below.
More details
on component materials
The composite material has been specifically designed
to have a low-reflection upper surface, and high-absorption lower
mass to absorb remaining sound energy. Sound energy is captured
and adsorbed, to a degree, within the upper acoustic foam layer.
Remaining sound energy reaching the very dense mass layer at the
base of the composite is then converted to thermal energy at a molecular
level. As this process occurs at a very small scale, and involves
very low levels of kinetic energy, so does not result in a noticeable
increase in the temperature of the composite.
Our
Acoustic Composite material has been tested to British Standard BS
476 Part 12 (1991) 'Method of test for ignitability of products by
direct flame impingement'. The following products have passed the Ignition Source A for 120 seconds - designed to represent
a possible end-use ignition hazard (i.e. first flame after electrical failure)
with the application of a flame at 45° for both surface burn and edge
ignition:
BS 476-12:1991 is an appropriate fire test for acoustic materials for application
inside PC and Server Enclosures. The test stipulates that 'where
materials will be fixed to substrates in practice, analogous procedures
shall be used to prepare test specimens'. During the above flammability
testing, soundproofing material samples were adhered to a solid
1mm steel plate and ignitability tested as if in situ,
rather than in free air (which does not occur in practice). For
more details see the BSI
Website.
Image showing the graphical results of two sound tests; one for the acoustic foam and another for the acoustic barrier mass. Both materials are used in Acousti Products. The acoustic foam (thickness 25mm) was tested using the test standard ASTM C384.
The results (shown as a black curve with scale on the left hand axis) show that the sound absorption sharply increases from approx 0.2 to approx 0.9 from 200Hz to 1000Hz, and then remains high, above 0.9 from 1KHz through to 7KHz. The acoustic barrier mass was tested using the test standard ISO R140. The results are displayed as Sound Transmission Loss (STL) in dB as a grey line (using the log scale on the right hand side of the graph). The STL remains high above 10dB throughout the frequencies tested from 100Hz to 4KHz. There is a marked increase in effective noise absorption from 200Hz to 500Hz, and from this point the STL remains above 20dB.
The test results show that the acoustic barrier mass has a relatively high sound absorption efficiency at the lower test frequencies and the acoustic foam 'optimal' sound absorption occurs above 1KHz.
The acoustic foam we employ is a charcoal grey professional semi-open cell studio-grade dense acoustic foam that is non-shedding and does not crumble or generate dust. This is approx. 60-65Kg/m³ - which is unusually dense compared to cheaper alternative noise-reduction foams. The reasons for selecting such a high-density foam are:
The acoustic foam is certified to the highest appropriate UL94 specification for a foamed product (UL94 HF1), and also ISO 3582, FMVSS 302 and DIN 4102 for low flammability, and can be operated normally within the temperature range -40°C to +100°C.
The dark grey/black flexible acoustic barrier mass is manufactured from an EVA-based polymer compound incorporating additional components to increase the product's mechanical strength, density, durability and fire resistance. Our uniquely developed acoustic barrier material is a non-PVC based compound that is bitumen free and therefore does not give off undesirable odours or vapours when warm. It is very dense at approx. 2,500Kg/m³, and does not contain unrefined aromatic oils, lead, chromium, cadmium, or mercury. It is designed to add mass to computer casing; for example, sheet aluminium, steel, alloys and non-glossy plastic surfaces. The mass of the material acts to absorb sound energy at a molecular level as an acoustic absorption barrier, significantly reducing noise transmission and also reducing any natural resonant frequencies of the substrate to which it is adhered.
The acoustic barrier mass is certified to international standards for extremely low flammability. We believe it is the most low flammable acoustic material for our application available on the market. Standards include FMVSS302 and ISO 3795 (Burn Rate B, <5mm/min). It can be operated normally within the temperature range -25°C to +80°C.
Acousti Products use non-flammable adhesives throughout our products. Our high temperature self-adhesive is less odorous than solvent-based adhesives in some alternative products. The adhesives we employ can be operated normally within the temperature range -20°C to +100°C. If the materials are applied lightly at first, and a mistake is made during positioning, our self-adhesive allows for the materials to be peeled off and then reapplied. The adhesives are 'set' by applying pressure and become more fast with time. Do not remove the materials once they have been firmly applied, as this will damage the self-adhesive.
Although the range of operating temperatures stated above are those published
by our raw material manufacturers - we strongly recommend
that materials are not placed directly against hot components. This is to
ensure that products are installed with optimal safety in mind and to help
maintain hardware longevity. Always read the printed instructions with each
product prior to installation.